Industrial Processing
SunSwitch Short-wave infrared heaters are used in the industrial processing because of their ability to provide precise, rapid, and energy-efficient heating, making it a valuable tool for optimizing production processes, improving product quality, and reducing operational costs in a variety of industrial applications.
- Precision heating for controlled heating of specific objects
- Reduce your energy costs by up to 70%
- No heat dispersion—does not drift away in a large open space
- Very low maintenance; elements can last 4000 hours
- Improve your EPC rating
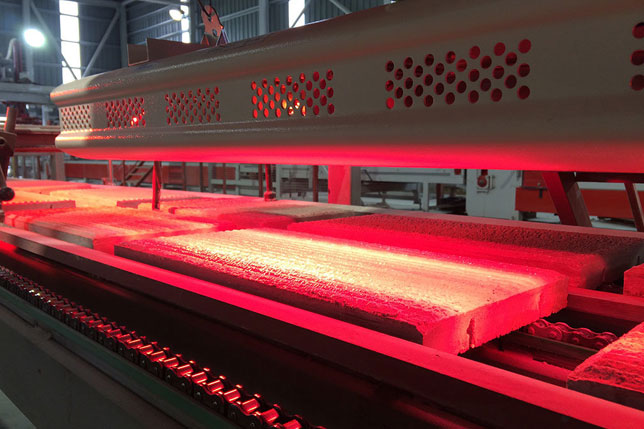
Upgrade your Industrial Processing Heating
SunSwitch only supply infrared heaters that are incredibly efficient and can save you up to 70% on your energy costs compared to traditional warm air heating systems.
Request a call back
Complete the form below to arrange a consultation with one of our experts.
Or call us on 01424 533215
Benefits of using infrared heating in industrial processing:
- Precision Heating: Sunswitch heaters emit focused, intense heat, allowing for precise and controlled heating of specific objects or areas within industrial processes. This precision is crucial in applications where accurate temperature control is essential for product quality and consistency.
- Rapid Heating: Sunswitch heaters produce high-intensity heat almost instantly, significantly reducing startup times in industrial processes. This is particularly valuable in applications where time-sensitive production is required.
- High Temperatures: Sunswitch heaters can achieve extremely high temperatures, making it suitable for applications that require intense heat, such as melting, welding, curing, and drying processes.
- Focused Heating: Sunswitch heaters can be precisely directed to the target area, minimising heat wastage and ensuring that only the intended objects or materials are heated. This reduces energy consumption and enhances process efficiency.
- Versatility: Sunswitch heaters are versatile and can be integrated into various industrial processes, including plastics processing, food manufacturing, glass production, and metalworking.
- Reduced Heat Loss: Sunswitch heaters emit radiant heat directly to objects and materials, which means there is minimal heat loss to the surrounding environment. This focussed heating approach ensures efficient and effective heat delivery.
- Clean Heat: Sunswitch heaters produce clean and odourless heat, making it suitable for use in industrial processes without causing air quality concerns or contaminating products.
- Durability: Sunswitch heater elements are robust and can withstand harsh operating conditions and environments, ensuring a long operational life and minimising maintenance requirements.
- Instant Control: Sunswitch heaters can be turned on and off instantly, providing precise control over the heating process. This enables rapid adjustments to temperature and minimizes energy consumption during idle periods.
- Uniform Heating: Sunswitch heaters can achieve uniform heating across large surfaces or materials, contributing to consistent product quality and reducing the risk of defects in industrial processes.
- Space Efficiency: Sunswitch heaters are reasonably compact and can be integrated into production lines, optimising space usage within the industrial process.
Because there is no dispersion of the heat SunSwitch infrared heaters are incredibly efficient and can save you up to 70% on your energy costs compared to traditional air heating systems.
Furthermore, SunSwitch electric heaters cost much less to buy and run than alternatives and are virtually maintenance-free. No contest!
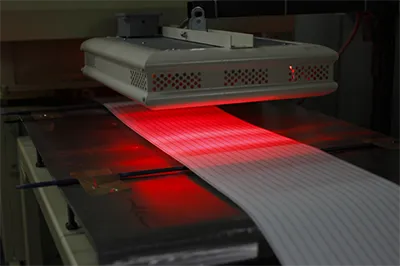
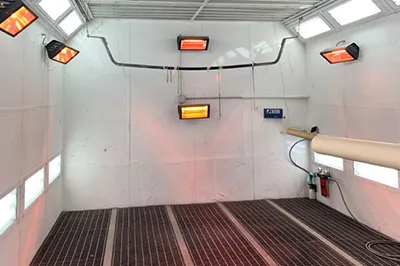
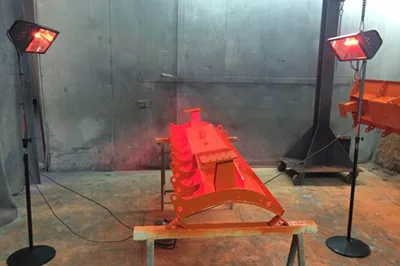
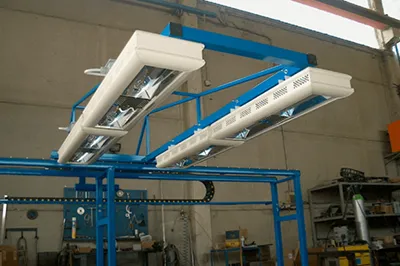
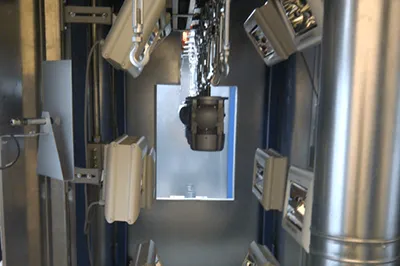
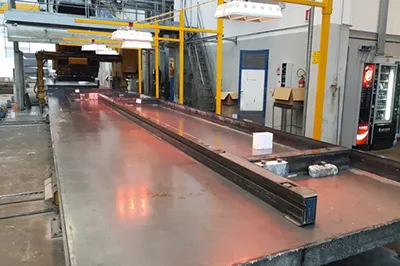
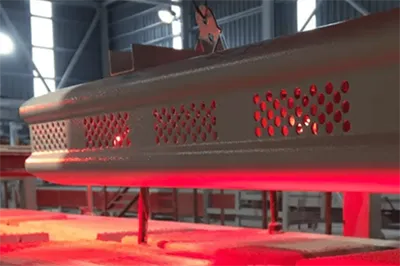
Infrared heaters from Star Progetti are in fact an efficient and economical solution for many industrial applications where targeted and adjustable heat is needed such as:
- Moisture removal
- Production of specific temperatures
- Drying of various materials, construction
- Ageing of materials
- Acceleration of bonding processes
- Heat treatment of materials prior to processing
- Drying water-based coatings
- Temperature-controlled plant maintenance
- Heat treatment of materials prior to processing
- Thermosterilisation
- Rapid drying of primers, sealants, marbles
- Construction of economical drying ovens Polymerisation of resins, inks